What is LSR Injection Molding?
Liquid Silicone Rubber (LSR) Injection Molding is a specialized manufacturing process used to produce flexible, durable, and high-performance silicone rubber parts. Unlike traditional rubber molding methods, LSR Injection Molding uses a liquid silicone material that is injected into a mold under controlled conditions of heat and pressure. Once inside the mold, the material is cured, creating a final product that is heat-resistant, biocompatible, and capable of withstanding harsh environmental conditions.
LSR Injection Molding is particularly valued for its ability to produce parts with complex geometries, thin walls, and high consistency across large production runs. It’s widely used in industries such as medical, automotive, consumer electronics, and food processing, thanks to its unique properties, including its resistance to extreme temperatures, flexibility, and long-lasting durability.
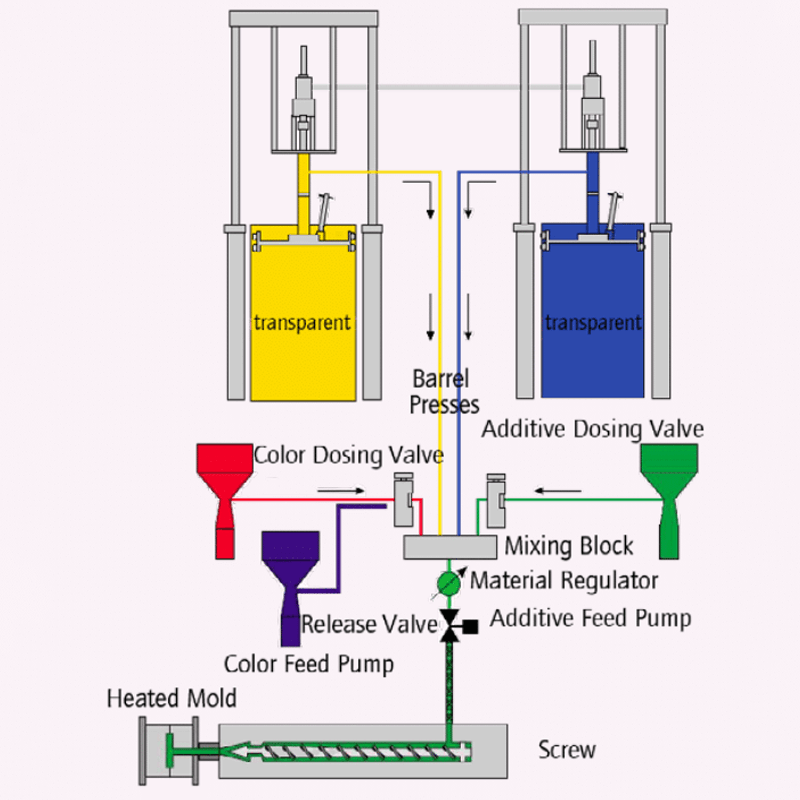
At Kitchenbathsilicone, we specialize in Liquid Silicone Rubber (LSR) Injection Molding, a process designed to deliver high-quality silicone products with precision, efficiency, and consistency. As a leading manufacturer in the silicone industry, we offer advanced capabilities that cater to a wide range of industries and applications. This page will outline the key aspects of our LSR injection molding capabilities, the benefits of choosing Kitchenbathsilicone, and the major fields where our expertise is applied.
Key Capabilities of LSR Injection Molding
Our LSR Injection Molding capability is built on state-of-the-art technology and industry expertise, allowing us to produce silicone parts that meet the highest standards of quality. Here are the core aspects of our capabilities:
- Precision Mold Design
- Automated Injection Systems
- Temperature and Pressure Control
- Material Expertise
- Complex Geometries and Thin Walls
- Post-Molding Processing
The LSR Injection Molding Process
At Kitchenbathsilicone, our LSR Injection Molding process is carefully designed to ensure the highest quality for every product we manufacture. Here's an overview of the key steps involved in our LSR injection molding production process:
1. Material Preparation
The LSR material is a two-part mixture composed of liquid silicone and a catalyst. These two components are stored separately and only mixed just before the injection process. This ensures that the silicone doesn’t start curing prematurely and retains its desired flow properties.
2. Injection into Mold
Once the silicone mixture is prepared, it is injected into a pre-heated mold using a specialized injection machine. The mold is typically made from high-grade steel or aluminum and is designed to form the exact shape and features of the final part. The liquid silicone flows easily into every cavity of the mold, allowing for the production of parts with complex geometries and fine details.
3. Curing and Molding
After the silicone is injected into the mold, it undergoes a curing process, during which heat and pressure are applied to cause the material to solidify. This stage ensures the silicone is fully set and achieves its optimal strength, elasticity, and other desired properties. The curing time can vary depending on the part’s size, thickness, and material composition.
4. Demolding
Once the silicone has cured, the mold is opened, and the part is removed. Our automated systems ensure precise and clean demolding, minimizing defects such as flashing or distortion.
5. Post-Molding Processing
After demolding, parts may undergo additional post-molding steps, including trimming, cleaning, and surface treatments to remove any excess material or enhance surface finishes. For specific applications, parts may also be assembled into larger systems or packaged according to client specifications.
Why Choose Kitchenbathsilicone for LSR Injection Molding?
At Kitchenbathsilicone, we stand out for several key reasons that make us the preferred choice for LSR injection molding:
Cutting-Edge Technology
We employ the latest advancements in injection molding technology, including fully automated systems and advanced material controls, to ensure precision and efficiency in every production run.
Customization and Flexibility
Whether you need a unique color, specific material properties, or a complex part design, we have the flexibility to meet your needs. Our customization capabilities extend from product design to post-molding services, providing you with a comprehensive solution tailored to your project.
Strict Quality Control
Quality is at the heart of everything we do. Our rigorous quality control processes include in-process monitoring, final inspections, and post-production testing to ensure that every part meets exacting standards for strength, durability, and safety.
Industry Certifications
We are ISO 9001 certified, meaning our processes are held to the highest international quality standards. This ensures that you can trust us to deliver products that meet both regulatory requirements and your specific needs.
Application of LSR injection molding in home kitchens
LSR is biocompatible and resistant to bacteria, making it ideal for medical devices and equipment. We produce components such as medical seals, gaskets, valves, and breathing masks that meet stringent healthcare regulations. Our facility is ISO 9001 certified, ensuring that all medical-grade parts are produced in a controlled, clean environment.
Custom Silicone Vegetable Preservation Bag
Overview Silicone vegetable preservation products help keep produce fresh for longer by creating an airtight and flexible seal. Made from […]
Personalized Silicone Dining Plate for Children Care Solution Factory
Description: Introducing our premium Personalized Silicone Dining Plate for Children Care Solutions, expertly crafted from 100% FDA-certified, food-grade silicone for […]
Customized High Quality Food Grade Silicone Basting Oil Brush Manufacturing
Overview: Customized High-Quality Food Grade Silicone Basting Oil Brushes are precision-engineered kitchen tools made from 100% FDA, LFGB, and SGS-certified […]
Silicone Air Fryer Liners with OEM Service Solution Suppliers
Description: Our Silicone Air Fryer Liners with OEM Service Solutions are engineered for exceptional durability and high-performance use in air […]
Customized Silicone Baking Gloves
Overview Silicone Baking Gloves are made from heat-resistant, food-grade silicone, offering superior protection for baking, grilling, and cooking. Featuring a non-slip, […]
Personalized Logo Silicone Food Grade Silicone Cake Mould Suppliers
Overview: The Personalized Logo Silicone Food Grade Cake Mould is a high-quality baking tool made from premium food-grade silicone, crafted through […]
Silicone Compression Molding Silicone Food Storage Bag for Kitchen Usage
Description: Our Silicone Food Storage Bags are meticulously crafted from premium, food-grade platinum-cured silicone, guaranteeing BPA-free, non-toxic, and eco-friendly properties. Produced using […]
Silicone Cooking Spatulas Factory
Overview Silicone Cooking Spatulas are made from food-grade, heat-resistant silicone, ensuring durability and safety for all types of cooking. They feature […]
LSR Injection Molding Silicone Snack Containers for Food Industry Factory
Description: LSR Injection Molding Silicone Snack Containers are high-performance, eco-conscious storage solutions designed for both convenience and sustainability. These containers […]
Silicone Collapsible Cups Manufacturer
Overview Designed for business and commercial use, these silicone collapsible cups offer a space-saving and eco-friendly solution for cafes, restaurants, […]
Custom Fordable Silicone Cups for Travel Application Factory
Description: Made from food-grade platinum-cured silicone, our collapsible silicone cups are expertly crafted using precision compression molding to ensure consistent thickness, […]
Custom Cocktails Silicone lce Tray
Overview This high-quality silicone ice tray is designed for professional bar and restaurant use. Made from food-grade, BPA-free silicone, it […]